Home
List your patent
My account
Help
Support us
SELF-LOCKING FASTENERS HAVING A SUPERIOR WITHDRAWAL RESISTANCE
[Category : - Construction Processes & Equipment]
[Viewed 1266 times]
YOUTUBE VIDEO LINK:
Link
THE PROBLEMS, CHALLENGES AND NEEDS THE FASTENERS MEETS
Joints with dowel-type fasteners are the most common fixings in different types of structures, such as wood, interior, masonry and concrete constructions or industrial applications. Dowel-type fasteners include bolts, screws, dowels, inserts, and nails. The main characteristic of this type of connections is a relatively good lateral load resistance. On the other hand, especially simple dowels have a generally inferior pulling out resistance.
Nails are the least sophisticated and most easy-to-use dowel-type fastening means. They are quick and straight impact-drivable into place, possibly by a simple percussive tool such as a hammer. Producing the least friction, smooth shank nails are the easiest to install, but also have the least ability to be gripped by the penetrated material, as the holding power of such impact-drivable dowel-type fasteners is generally achieved by pressure and friction of displaced penetrated material bearing down on the shank of the fastener.
In wood constructions subjected to moisture changes from normal atmospheric variations, the withdrawal resistance of smooth-shank nails also diminishes in time. The withdrawal loads for plain nails driven into wood that is exposed to wide alternating changes in moisture content may be reduced as much as 75 percent below the original values soon after driving.
Moreover a drawback of similar impact-drivable dowel-type fasteners can be a repeatedly applied external loosening force or vibration of the construction, to which the fasteners are applied, which will also loose them with the lapse of time, thereby reducing the strength and the reliability of the joint. Another possible undesirable consequence of the fastener’s loosening is the squeaking of the connection, which is especially problematic in flooring and subflooring constructions.
Differently from common nails, a screw creates a superior interlocking joint with the penetrated material, that has a greater holding power, but as torque driven, is more complex and demanding to install. In order to retain its original advantages, especially the installation easiness, many particular types of nails have been developed for ordinary or special uses. To create a screw-like interlocking joint, having an improved holding power and supplying a higher resistance to withdrawal than provided by the common nail, the shanks of some nails are ringed, threaded, spiraled, and/or barbed.
A problem with the known ringed or barbed dowel-type fasteners is that, besides a higher withdrawal resistance form, they generally have also a greater driving-in resistance, wherein the higher required driving force results in a higher penetrated material’s destruction to weaken the fasteners holding power. In this aspect, its penetration resistance fundamentally limits the final pulling out resistance of the dowel-type fastener. Differently, the penetration of a smooth spiraled dowel-type fastener is less resistant and destructive. Thus, some combinations of spiraled and barbed known concepts try to get the best of both worlds with limited success.
While penetrating, the spiral fastener interacts with the penetrated material, mainly by its leading surfaces and most forcefully at the spiral ridgelines. Hence, the known screwed and ringed or barbed shank dowel-type fastener combinations, having rough, notched or serrated leading surfaces and ridgelines impact a high penetration’s resistance and penetrated material’s destruction, which serves poorly the overall fastener’s pulling out resistance. Thus, the presented improved spirally ridged self-locking dowel-type fastener is developed to overcome the known fasteners limitations and increase the fastening holding power and reliability.
As another particularly challenging aspect, there is in some cases a necessity to produce blind joints, so that the fastener itself is invisible after the joint has been formed. In high-quality furniture and other special constructions for example, the appearance of exposed mechanical fasteners such as nails, bolts, or screws is inappropriate. Although usual nails, bolts, and screws are generally exposed and visible, there are many prior art solutions of special inserts and double-ended impact-drivable dowel-type fasteners that can be concealed into a blind joint.
As the known double-ended fastener and insert nut solutions were limited by its prior art context, the improved impact-drivable dowel-type fastener concept is also the perfect solution to the double-ended fastener’s and insert nut’s joint, especially blind joint, production.
THE FASTENER'S FEATURES
The spirally ridged self-locking dowel-type fastener’s inventive concept takes a different approach from that taken by known fasteners, and it is grounded upon different principles to the prior art. It originates from a broader understanding of the elastic-plastic interaction between an impact-drivable dowel-type fastener and a receiving member. It employs this understanding to provide a distinct fastener, having an optimized shape, to achieve a less resistant, non-destructive penetration, a considerably stronger fastening interaction, and a higher axial withdrawal strength, over that of other known configurations.
The fastener has a functionally formed lateral surface, comprising a plurality of parallel spiral ridges defined by pairs of leading and trailing slopes. The leading slopes are generally smooth surfaces, spanning between a channel bottom and a smooth spiral ridgeline, designed to slide the fastener into a penetrated receiving member. The trailing slopes, on the other hand, have a rough, barbed or toothed, form designed to bite the receiving member into a locked position.
The fastener’s shape efficiently harnesses the different forces, actions and reactions, taking part in its introduction into a receiving member. An axial direction thrust, as a primary external force applied to the fastener, propels it into the receiving member. In the following collision, most of the fastener’s impact forces exert on its ridgelines and leading slopes. As a result, the sharp and smooth spiral ridgelines cut a channeled way and guide the fastener into the penetrated material. The smooth leading slopes’ impact into the substrate transfers part of the axial direction thrust energy into a useful elastic deformation of the fastener and receiving member system. The elastic deformation dilates the receiving material’s entering channels, thus releasing the trailing slopes and opening the way to the fastener’s insertion. As the impact overcomes the static friction between the fastener and the substrate, the fastener slides inside the receiving member. The smooth leading surfaces and smooth spiral ridgelines minimize the slide’s friction and the penetrated material destruction. As the fastener slides, a system’s elastic reaction prevails, returning the deformation toward its original shape and closing the entering channels. In the process part of its elastic energy transfers into a secondary reaction that axially spins the fastener and forces the toothed trailing part of the spiral formation to firmly bite the receiving member into a locked position. Ideally, the inward pushing motion causes minimal energy dissipation, so that most of its energy transforms in the twisting and gripping reaction of the fastener. The result of the said introduction is the interlocking of the fastener with the receiving member in a deeper and rotated position. The described introduction can be a single procedure or it can be easily repeated, until reaching the final fastening position.
The strong, non-destructive interaction creates a fastener’s superior withdrawal resistance and a high load capacity. Any additional shocks, vibrations or pulling out forces tend to engage the toothed trailing part of the fastener, increasing the bite into the penetrated material and reinforcing its fastening grip over a long run. As the axial pulling out force does not transfer into a torque needed to unlock the fastener from its locked position, an easy disengagement and fastener’s extraction is only possible by applying an intentional axial rotation to the fastener.
The fastener may assume many alternative variations and embodiments.
Patent publications:No publication
Asking price:
Make an offer
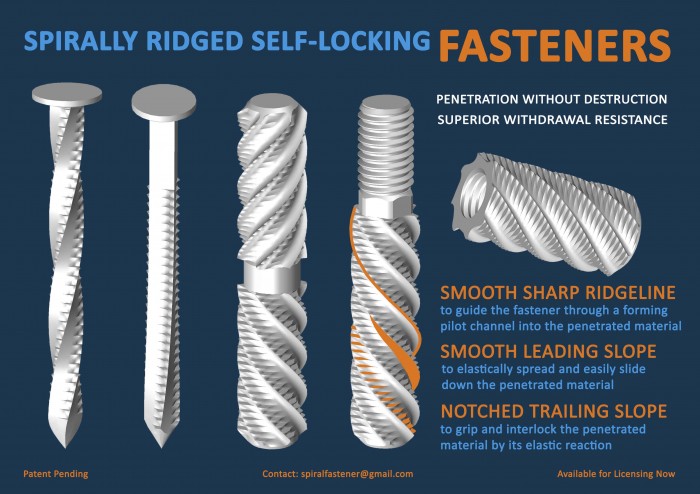
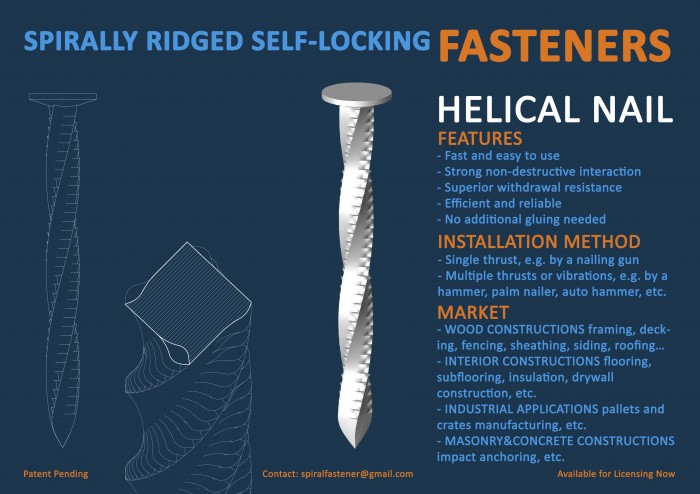
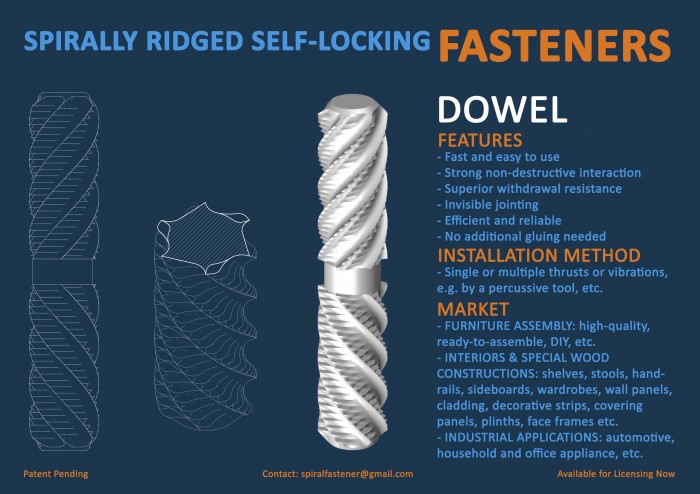
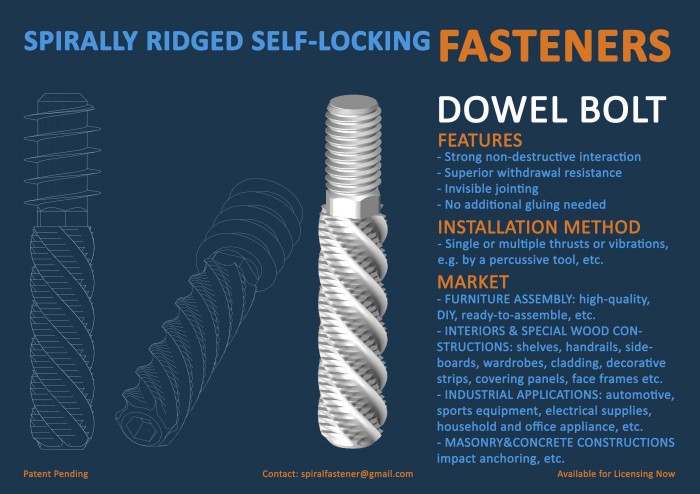
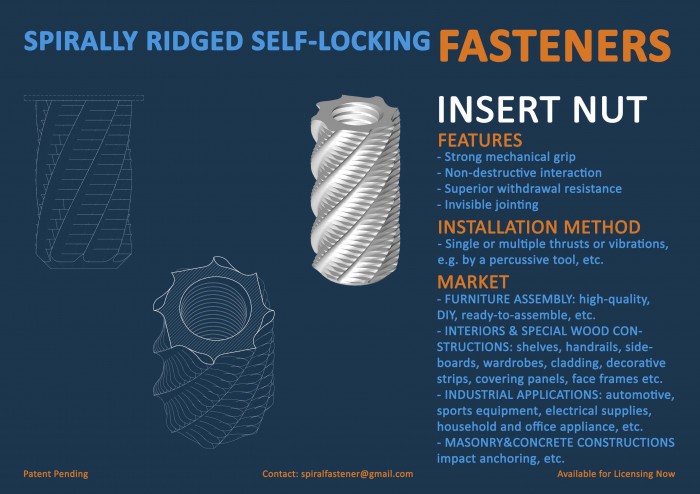
[ Home
| List a patent
| Manage your account
| F.A.Q.|Terms of use
| Contact us]
Copyright PatentAuction.com 2004-2017
Page created at 2025-08-18 5:03:48, Patent Auction Time.