Home
List your patent
My account
Help
Support us
Eco-Friendly Multifunctional GauzeBag Patent – Zero Waste Design
[Category : - HUMAN NECESSITIES- Cleaning devices- Baby products]
[Viewed 3274 times]
*This patented invention revolutionizes the reusable bag market by offering a multifunctional, eco-friendly, and sustainable solution with
Sustainability in Every Thread.
Designed with zero-waste production principles, it addresses the global demand for alternatives to single-use plastic bags.
Key Features:
Multifunctionality: Acts as a grocery bag, cleaning cloth, mop refill, and more.
Zero-Waste Design: Innovative handle integration eliminates fabric waste during production.
Eco-Friendly Material: Made of biodegradable gauze fabric, aligning with circular economy goals.
Lightweight and Durable: Weighs just 0.7 oz and carries up to 17 pounds ( 8 kg) of groceries.
Market Opportunity:
Cost-effective manufacturing at $0.25/ unit
The reusable bag market is projected to reach $14 billion by 2027, driven by government bans on plastic bags and consumer demand for sustainable products.
Ideal for companies in the eco-friendly, home goods, or retail sectors looking to expand into sustainable product lines.
Why Buy This Patent?
Tap into the growing eco-conscious consumer base.
Gain a competitive edge with a patented, versatile design.
Position your company as a leader in sustainability.
Photoa of this "All in One" product can be seen on the link below.
Link
Financial informationOpen to selling the patent outright, licensing the rights with royalties, or some other form of partnership.
Asking price:
Make an offer
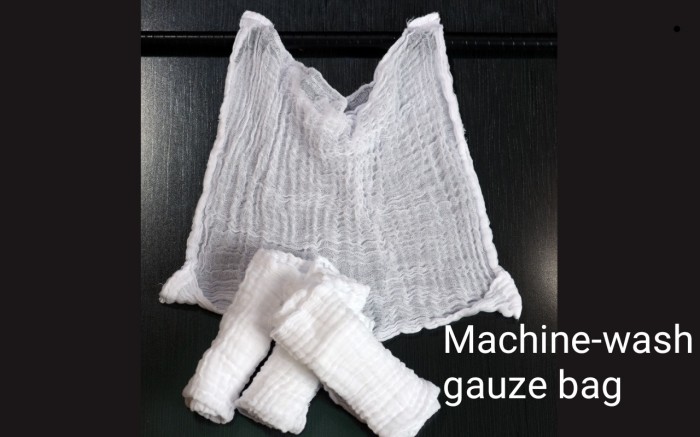
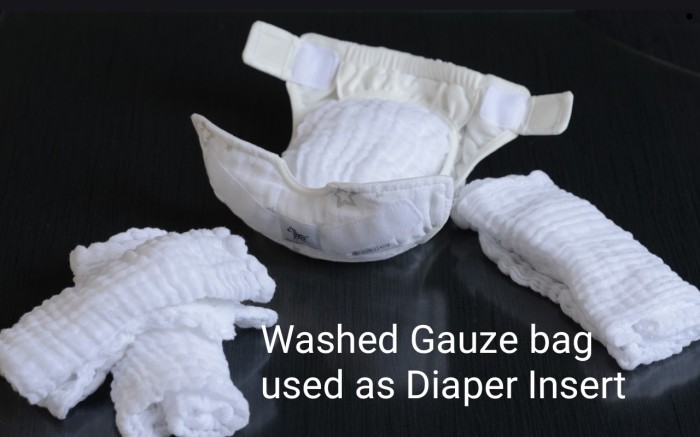
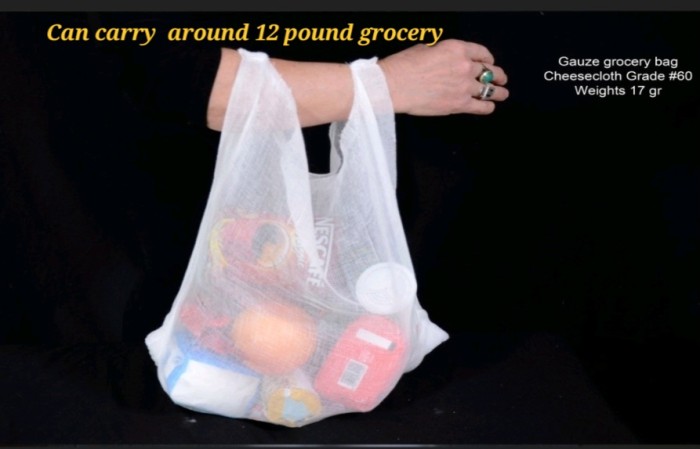
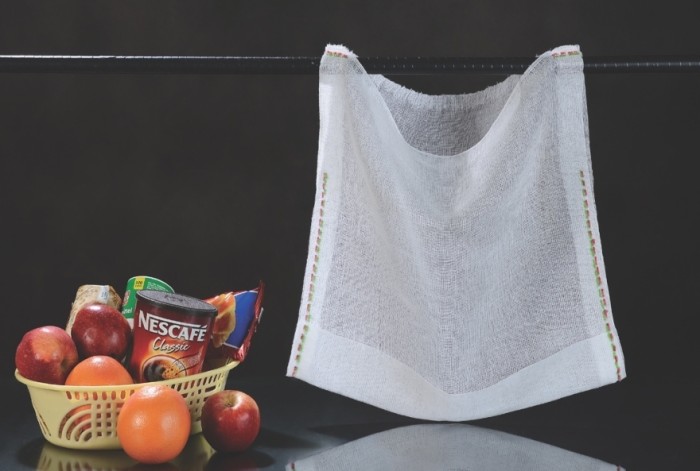
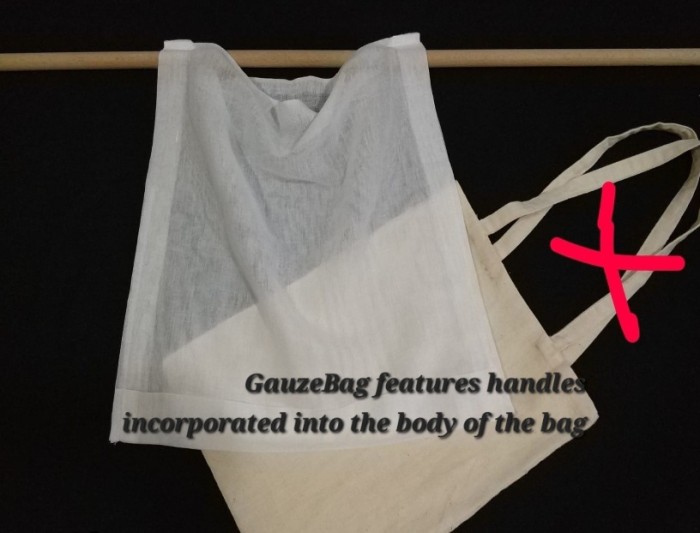
[ Home
| List a patent
| Manage your account
| F.A.Q.|Terms of use
| Contact us]
Copyright PatentAuction.com 2004-2017
Page created at 2025-08-17 21:27:20, Patent Auction Time.