Home
List your patent
My account
Help
Support us
SYSTEM FOR REMOVING HARDENED LUBRICANT FROM AN ENCLOSED GEARBOX
[Category : - OTHER]
[Viewed 292 times]
My name is Roy Aldridge and I am a Horizon Valve Services Inc Division manager and the inventor of the CorFlush System gearbox flushing unit. This unit is fully patented and now I am one of two owner’s of the CorFlush Systems LLC which is a Division of Horizon Valve Services Inc. In 2002 one of our tank farm customers requested our company to explore the possibility of cleaning his enclosed gearboxes in electric valve actuators as well as handwheel operated, of the old grease and replacing it with new without removing it from the product line. Here are the problems he said he was facing: (PROBLEM) Downtime was his number one enemy. In an environment where equipment is expected to run 24 hours a day 7 days a week under extreme conditions, it is paramount to have all equipment well lubricated to prolong reliability. One of his problems was the number of Limitorque SMB, SM, SMC, and even HMB valve actuators that have been in operation since the 1950’s and due to the extreme conditions under which they are used, the grease in the enclosed gearbox loses its moisture and becomes dry like clay. When grease becomes dry it loses its ability to release its oil (oil bleed) during operation to properly lubricate the bearings and gears in the enclosed gear box. When technicians are instructed to maintenance a gearbox, they simply pump more grease in, however too much grease volume (over greasing) in a bearing cavity will cause the rotating bearing elements to begin churning the grease, pushing it out of the way, resulting in energy loss and rising temperatures. This leads to rapid oxidation (chemical degradation) of the grease as well as an accelerated rate of oil bleed, which is a separation of the oil from the thickener. The heat that has been generated over time along with the oil bleed eventually will cook the grease thickener into a hard crusty build-up that can impair proper lubrication and even block new grease from reaching the core of the bearing. This can result in accelerated wear of the moving internal elements and then component failure. Seal damage is another negative side effect of over greasing. Grease guns can produce up to 15,000 psi, and when you over grease a bearing housing, the lip seals can rupture, allowing contaminants such as water and dirt to gain access into the bearing housing. Keep in mind that lip seals usually fail around 500 psi. (SOLUTION) The CorFlush System will revive the life of your electric actuators and other gear boxes and operators that will greatly reduce equipment failure before it happens. Plus, there will be no need for the line to be shut down. CorFlush will clean your actuator’s gear box and replenish with the recommended grease or oil, extending the life of the actuator gearbox while still in line and in service.
The following is how the CorFlush System will achieve this: • “Heated” CRX-98 flushing agent is our proprietary blend designed and patented to break down the hard clay-like grease to the point of it being flushed out of the gearbox.
• We have 4 different units that Flushes a variety of actuators and gearboxes in-line without removing them from service by a new method of low pressure – high volume internal flush process.
• Requires 2 facility trained technicians. • Will maintenance multiple actuator gearboxes per day. • One unit can maintenance 2 actuator gearboxes at the same time. • Removes all residues, water, dirt, metal shavings and hardened grease allowing lubrication replacement for extended life of your actuator gearbox.
• After contaminates are removed from gearboxes they can be analyzed to see what issues you are having, whether it is outside particles getting in or worn parts created inside needing to be taken out. • Excellent for winterizing and preventing corrosion of actuators and gearboxes by removing water. • Assist in conforming to DOT (Subchapter D – Pipeline Safety) 49 CFR 192.745.192.747 and CFR 195.116.195.420 which states that all actuators must be operated a minimum of every 15 months. • Offers a Huge 94% savings on maintenance cost per actuator/gearbox.
I have videos of the equipment working in gas, oil, and electric power if you are interested, I can email to you.
Financial informationOn one of our 1st endeavors in the power generating world, we quoted for the local electrical power generating station near Tulsa, Oklahoma. I quoted for 5 days of flushing out electric mov's or the electric valve operators which have the enclosed gearboxes. We flushed the gearboxes and once cleaned we refilled with oem grease or oil. After the 5 original days quoted the plant maintenance manager, (who offered to recommend our services) asked me to tear up my original quote because he wanted us to try flushing some other equipment for him. We flushed a large preheater boiler which took 2 days, and then a bank of cooling towers. After finishing the added work we went from the original quote of $30,000 to $97,000 and a total of 5 weeks. After this plant, covid hit and we couldn't even visit the plants so, here I am without my original crew and starting over. We have never done a live demonstration that this system wasn't highly appreciated. There is competition for oil flushing but none at all for hard grease. flushing.
Asking price:
Above 1 million USD
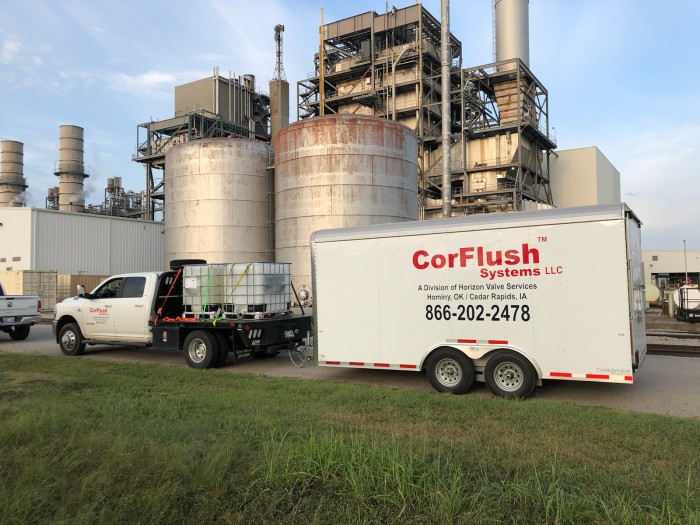
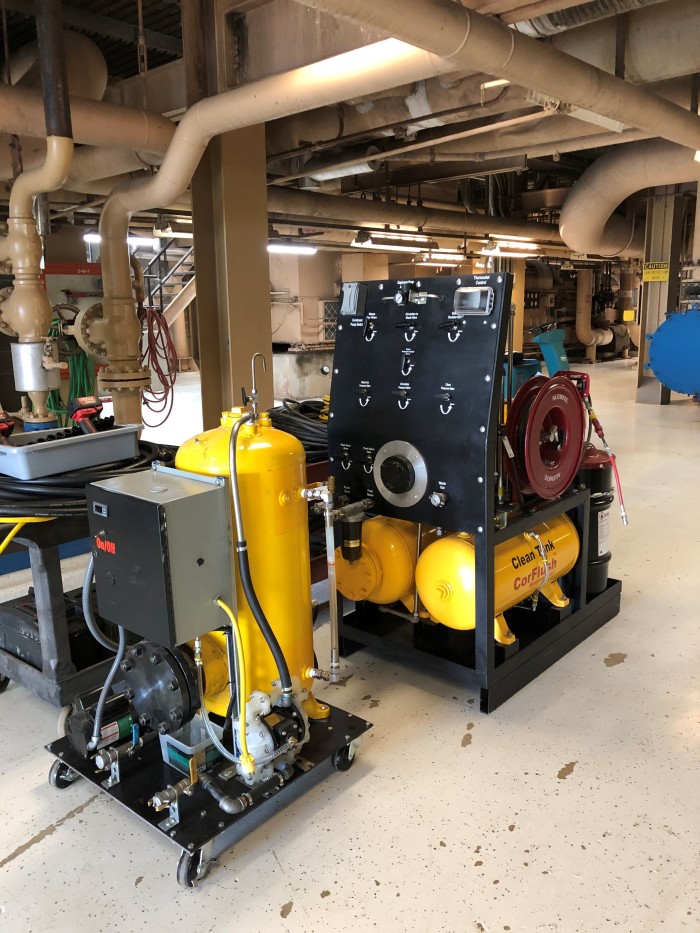
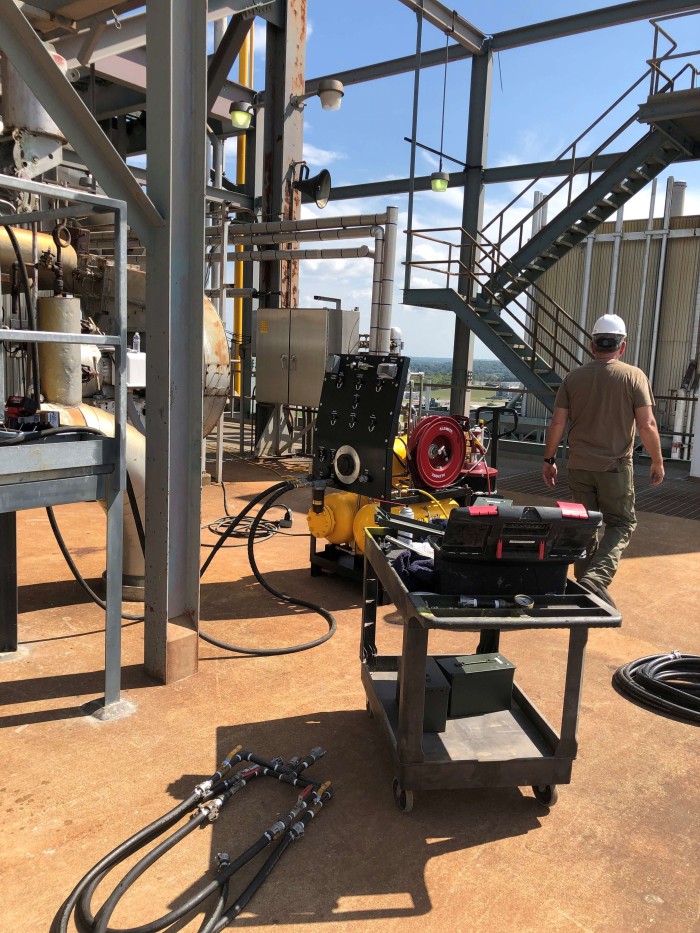
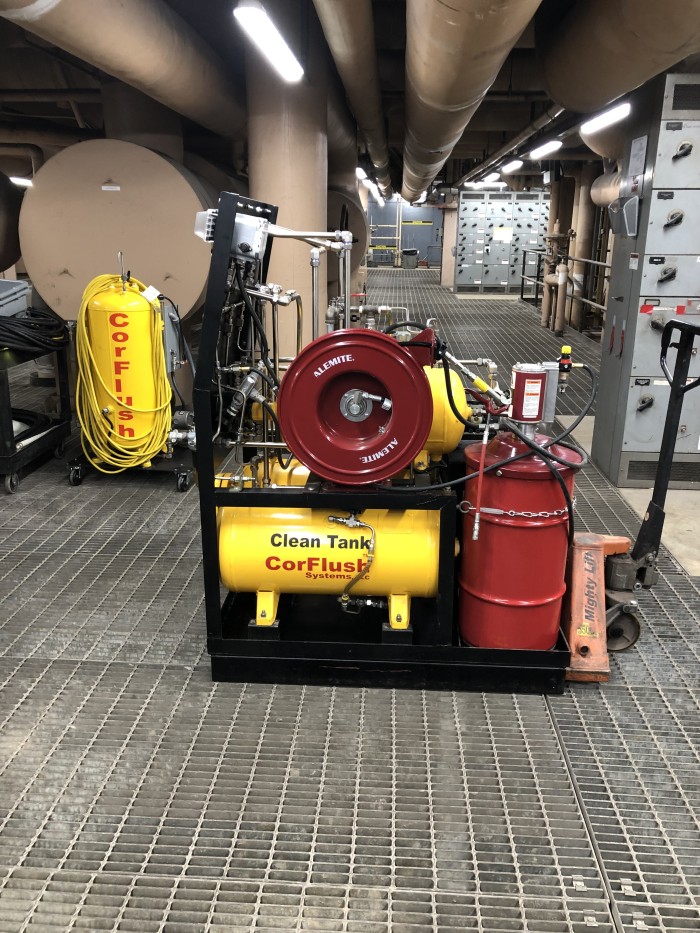
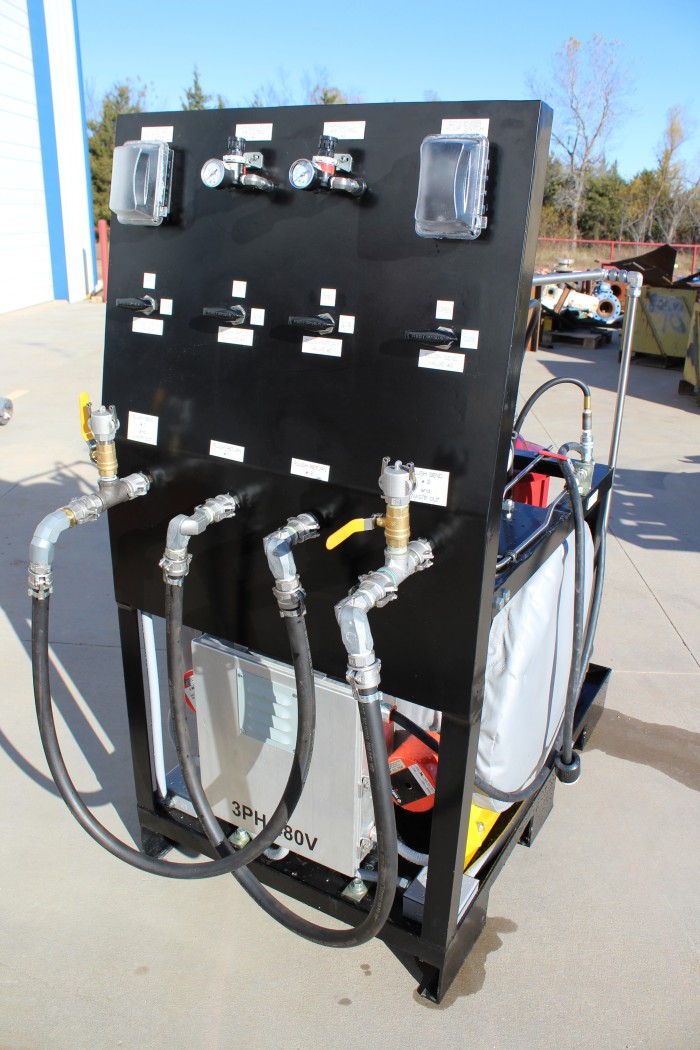
[ Home
| List a patent
| Manage your account
| F.A.Q.|Terms of use
| Contact us]
Copyright PatentAuction.com 2004-2017
Page created at 2025-08-24 16:46:53, Patent Auction Time.